厚钢板焊接常见缺陷及预防
根据您提供的文本内容,厚钢板焊接过程中的常见缺陷包括**气孔、夹渣、未焊透和裂纹等**。为预防这些缺陷,可以采取以下措施:,,1. **表面清理**:在焊接前彻底清除钢板表面的锈迹、油污及氧化皮,确保钢板表面无杂物和凹凸不平。对于切边钢板,边缘应处理平滑,无锯齿形或深度不大于2mm的个别发纹。, ,2. **内部气体处理**:检查并处理板坯内部聚集的气体,如皮下气孔或气泡,避免在焊接时气体不能焊合造成的缺陷。,,3. **设计优化**:在钢结构深化设计阶段,通过节点设计减少焊接应力集中,避免或减少使母材板厚方向承受较大的焊接收缩应力。,,4. **坡度过渡处理**:在焊缝高出薄板厚度处,应将焊缝焊成斜坡状,最大允许值为1:2.5;或在焊接前加工成斜坡,坡度最大允许值为1:2.5。,,5. **多层焊接连续性**:多层焊接时,应注意不连续,以避免冷裂纹的产生。,,6. **现场处理**:对超出规定厚度的钢板进行特殊处理,比如在高出薄板厚度处进行斜坡焊接,以减少应力集中和未熔合等缺陷。,,7. **机械加工**:对于直接承受动载荷且需要进行疲劳验算的结构,斜坡坡度不应大于1:4,以保证焊接接头的稳定性。,,8. **热切割与砂轮打磨**:当采用热切割或机械加工无法实现平缓过渡时,可采用砂轮打磨的方法来达到所需的坡度要求。,,9. **焊接工艺选择**:选择合适的焊接方法,如手工电弧焊、气体保护焊等,以适应不同材料和结构的要求。,,10. **焊接参数优化**:调整焊接电流、电压、速度等参数,确保焊接过程稳定,避免因参数不当导致的缺陷。,,厚钢板焊接中常见的缺陷及其预防措施主要包括气孔、夹渣、未
厚钢板焊接常见缺陷及预防
厚钢板焊接过程中可能会遇到多种缺陷,这些缺陷可能会影响焊接质量,甚至导致结构安全隐患。以下是厚钢板焊接的一些常见缺陷及其预防措施:
1. 未焊透
原因分析:未焊透通常是由于对口间隙过小、坡口角度偏小、钝边厚、焊接线能量小、焊接速度快、焊接操作手法不当等原因造成的。
预防措施:
- 严格执行标准要求,确保对口间隙不小于2㎜。
- 根据壁厚选择合适的坡口类型,如壁厚小于20㎜的焊口采用V型坡口,单边角度不小于30°;不小于20㎜的焊口采用双V型或U型等综合性坡口。
- 选择合适的线能量、焊接速度和操作手法。
- 使用短弧焊接,以增加熔透能力。
2. 未熔合
原因分析:未熔合可能是由于固体金属与填充金属之间(焊道与母材之间),或者填充金属之间(多道焊时的焊道之间或焊层之间)局部未完全熔化结合,或者在点焊(电阻焊)时母材与母材之间未完全熔合在一起。
预防措施:
- 适当加大焊接电流,提高焊接线能量。
- 焊接速度适当,不能过快。
- 熟练操作技能,保持正确的焊条(枪)角度。
3. 气孔
原因分析:气孔是在熔化焊接过程中,焊缝金属内的气体或外界侵入的气体在熔池金属冷却凝固前未来得及逸出而残留在焊缝金属内部或表面形成的空穴或孔隙。
预防措施:
- 焊条进行烘培并装在保温筒内,随用随取。
- 焊丝清理干净,无油污等杂质。
- 焊件周围10~15㎜范围内清理干净,直至发出金属光泽。
- 注意周围焊接施工环境,搭设防风设施,管子焊接无穿堂风。
- 氩弧焊时,氩气纯度不低于99.95%,氩气流量合适。
- 尽量采用短弧焊接,减少气体进入熔池的机会。
- 合理操作手法,焊条、焊枪角度合适。
- 合适的焊接线能量,焊接速度不能过快。
- 按照工艺要求进行焊件预热。
4. 夹渣与夹杂物
原因分析:夹渣与夹杂物是指熔化焊接时的冶金反应产物,例如非金属杂质(氧化物、硫化物等)以及熔渣,由于焊接时未能逸出,或者多道焊接时清渣不干净,以至残留在焊缝金属内。
预防措施:
- 焊件焊缝破口周围10~15㎜表面范围内打磨清理干净,直至发出金属光泽。
- 多层多道焊时,层间药皮清理干净。
- 焊条按照要求烘培,不使用偏芯、受潮等不合格焊条。
- 尽量使用短弧焊接,选择合适的电流参数。
- 合适的焊接速度,不能过快。
5. 裂纹
原因分析:裂纹是焊接过程中或焊接完成后在焊接区域中出现的金属局部破裂的表现。
预防措施:
- 控制焊接参数,避免焊接过程中产生过大的应力。
- 采用合理的焊接顺序,减少焊接变形。
- 对于厚板焊接,应加强对层间温度的控制,避免层间温度过高或过低。
6. 焊接变形
原因分析:焊接变形是由于焊接过程中金属的热膨胀和收缩引起的。
预防措施:
- 在焊接之前,应根据钢板的性质和厚度,确定合适的焊接参数,尽量控制焊接时间和温度。
- 采用合理的焊接顺序并选用合适的焊接规范和操作方法。
- 采用反变形和刚性固定措施。
通过以上措施,可以有效地预防厚钢板焊接过程中可能出现的各种缺陷,确保焊接质量和结构安全。
厚钢板焊接应力控制技巧
厚钢板焊接变形矫正方法
厚钢板焊接热影响区处理
厚钢板焊接质量检测技术
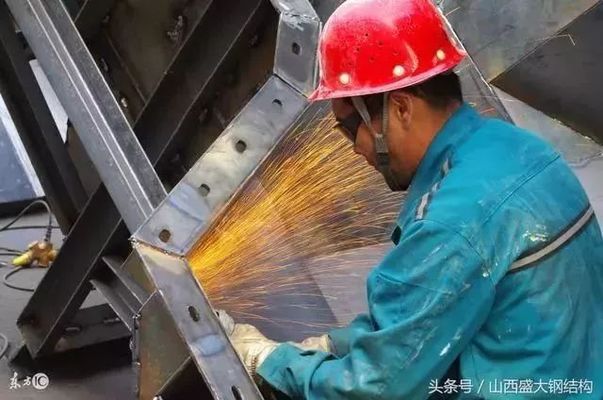
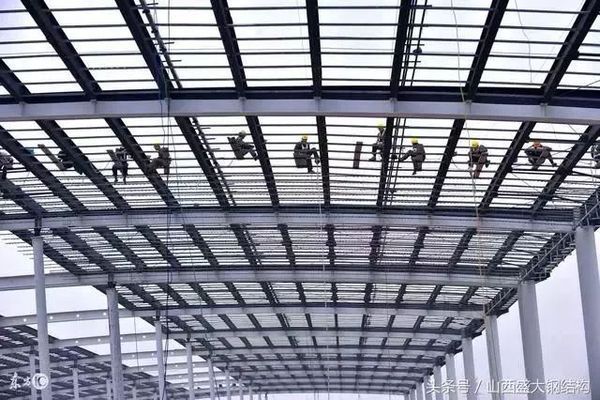
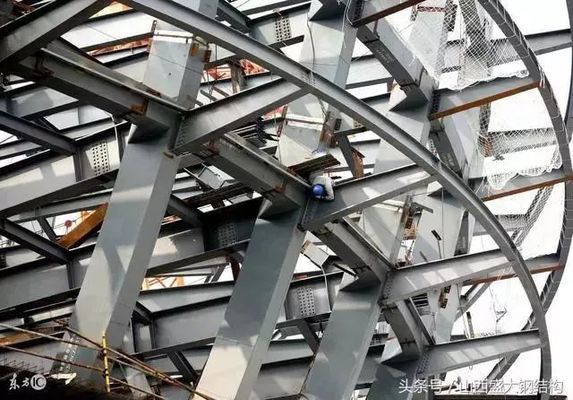
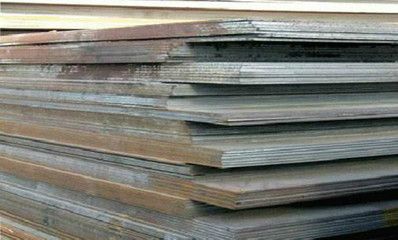

还没有评论,来说两句吧...